
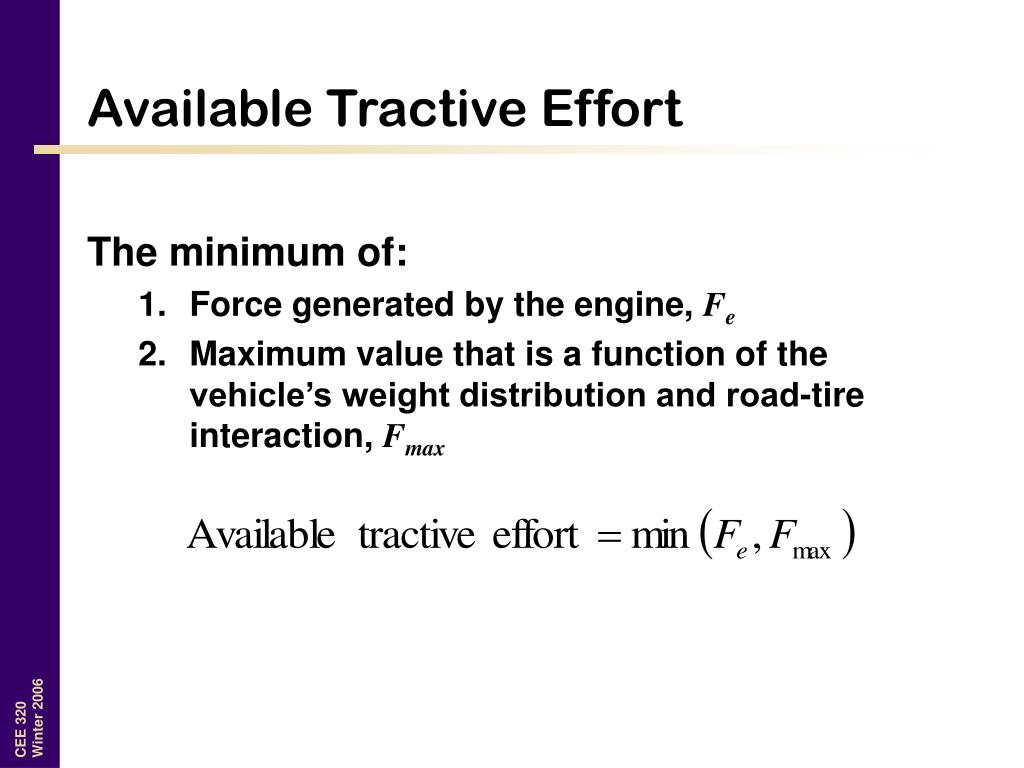
Excluding prototype models, the drag coefficient in this list ranges between c = 0.25 for the Honda Insight to c = 0.58 for the Jeep Wrangler TJ Soft Top. On you can find a table of drag coefficients for many common modern car models. In general, you want to have this value as low as possible. You probably don’t know this value for your car and there’s a good chance you will never find it out even if you try. This is the one quantity in this formula that is tough to determine. With c (dimensionless) being the drag coefficient. Of course there’s also the dependence on the velocity v (in m/s) relative to the air. We also need to know the projected area A (in m²) of the car, which is just the product of width times height. One of these is the air density D (in kg/m³), which at sea level has the value D = 1.25 kg/m³.
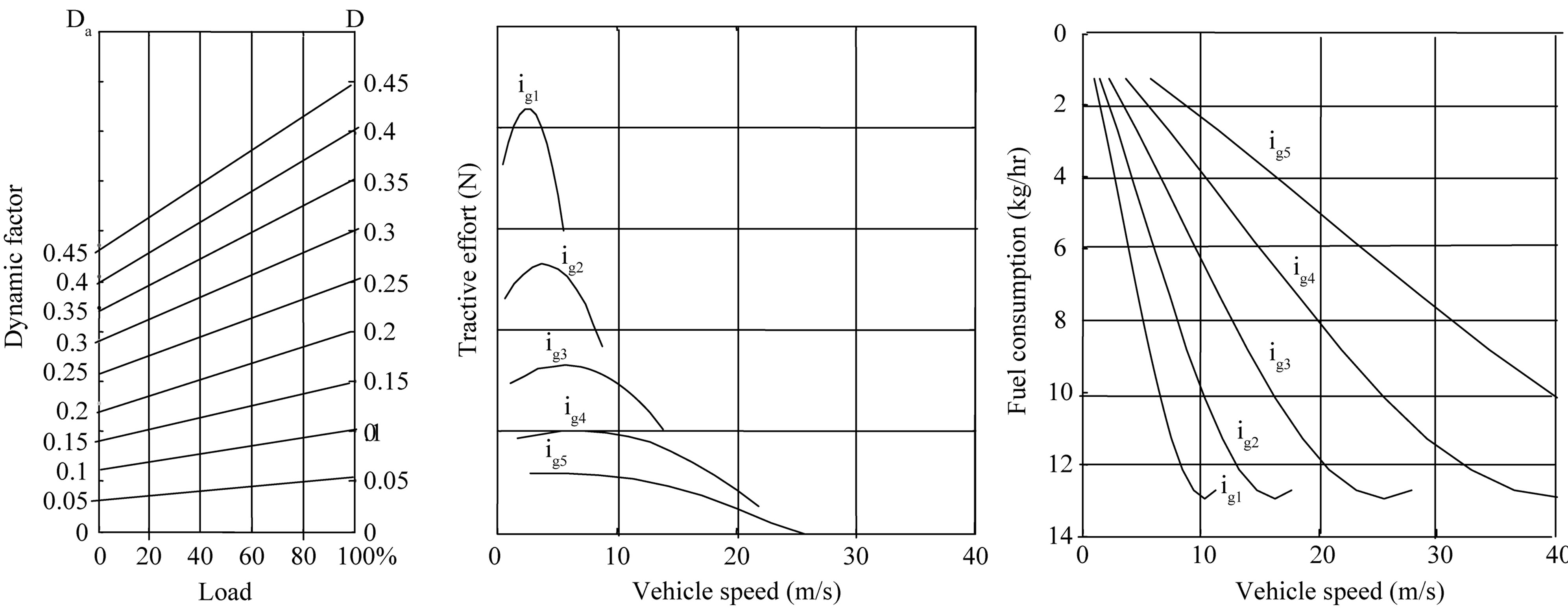
To compute air resistance we need to know several inputs. This makes things considerably easier for us. However, in our case looking at the latter is sufficient since at high speeds, air resistance becomes the dominating factor. Obvious candidates for the retarding forces are ground friction and air resistance. Our first job is to find out what forces we are dealing with. The force that is aiming to accelerate the object is exactly balanced by the force that wants to decelerate it. You probably know that whenever a body is moving at constant speed, there must be a balance of forces in play. The problem with this option is that there’s not always an Autobahn nearby. The stability of a vehicle can be controlled by the dynamic performance analysis.How do you determine the maximum possible speed your car can go? Well, one rather straight-forward option is to just get into your car, go on the Autobahn and push down the pedal until the needle stops moving. The dynamic performance of the vehicle are depends on the road conditions and driving maneuver.

A rural route is set to launch the experiment and the road conditions are determined for the test. The COG of the vehicle is determined by using the weight of the vehicle. The experiment starts with weighing a car model to get the center of gravity (COG) to place the accelerometer sensor for data acquisition (DAQ). The experiment is done using the accelerometer to record the reading of the vehicle dynamic performance when the vehicle is driven on the road. effect of vehicle based on roll, pitch, and yaw, longitudinal, lateral and vertical acceleration. Real driving experiment on the vehicle is conducted to determine the. This paper emphasizes the analysis of vehicle dynamic performance of a real vehicle. The dynamic behaviours are determined by the forces from tire, gravity and aerodynamic which acting on the vehicle. Vehicle dynamic is the effects of movement of a vehicle generated from the acceleration, braking, ride and handling activities. As the EReSS is proven to harvest energy, it can be used on hybrid and electric vehicle to improve the efficiency of the vehicle and reduce the fuel consumption. The voltage output of the EReSS can be optimized by setting up the parameters. The number of windings of the coil and diameter of the coil affect the voltage output of the EReSS. It is observed that the EReSS can harvest the wasted energy from the vibration and produce sufficient electric energy for the vehicle electri-cal and electronic usage. A prototype of electromagnetic EReSS is fabricated and laboratory experimentation on test rig is conducted to test the voltage output. The harvested energy is converted to electrical energy for vehicle usage. system (EReSS) as a system that harvests energy from the vibration of vehicle suspension system. This paper emphasizes the development of electromagnetic energy regenerative suspension. The vehicles use different energy other than fuel which is electric energy. The en-ergy efficient vehicle (EEV) is one of the advancement for future land transportation that known as hybrid and electric vehicles nowadays.

The world is demanding for alternative way of energy consumption for vehicle usage.
